I took a picture of three different samples sewn on the same serger. The tension was set exactly the same on each one.
On the sample on the left, the edge of the fabric is curled. The sample in the middle, the looper threads go too far beyond the edge of the fabric. To correct both problems, I did not fiddle with looper tensions. I simply changed the width to which the fabric was cut.
For the left one, I decreased the cutting width, which pulled the fabric away from the edge of the threads. For the middle one, I increased the width, which brought the fabric out to the edge of the threads.
I let the fabric determine for me, where to set the cutter. This is much easier than playing with tension.
The sample on the right was easily achieved using this method.
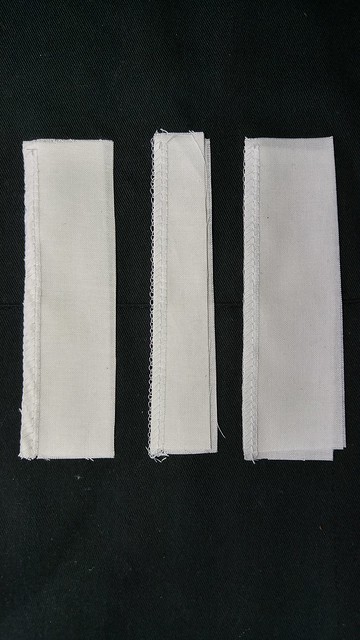